Granulerad masugnsslagg och kalksten ersätter mängden cementklinker med cirka 30 procent i Viridiscement*. Nivån fördelas på cirka 21 procent slagg, som är en produkt från ståltillverkningen, och cirka 9 procent kalksten. Den höga inblandningen av slagg och kalksten leder till en utmärkt hållbarhet och bra hållfasthet.
– Vi har vidareutvecklat en bra produkt genom att öka andelen slagg och kalksten. På så sätt har vi sänkt klinkerfaktorn som skapar koldioxidutsläppet. Det fina resultatet har också nåtts tack vare en hög andel alternativt bränsle under cementklinkertillverkningen, förklarar Urs Müller som är teknisk chef vid Schwenk Sverige AB.
– Nu tar vi steget fullt ut och förbättrar två bra produkter med en bättre: Komposit och Miljö blir Viridis, understryker Tomasz Borowiec vd för SCHWENK Sverige AB.
Nu tar vi steget fullt ut och förbättrar två bra produkter med en bättre
tomasz borowiec, vd schwenk sverige ab
Hållbarhetskoncept
Urs Müller berättar att företaget har som mål att leda utvecklingen mot allt grönare produktion. Sveriges byggsektor ställer allt högre krav på miljöanpassade produkter och det betyder att SCHWENK som cementtillverkare strävar efter att utveckla nya koncept inom processteknologi och cementsammansättning för att sänka miljöpåverkan av framtida produkter.
Siktet är redan inställt på framtiden genom ett antaget hållbarhetskoncept:redan 2023 minskades det genomsnittliga klimatavtrycket av klinkertillverkning med 50 kilo per ton. Det var två år före SCHWENKs tidigare uttalade mål på området. Reducera genomsnittlig klinkerfaktor med tio procent till 2025. Första klimatneutrala fabrik 2030.
Koldixoid för lagring och användning
EU kommer från 2026 att reducera andelen kostnadsfria utsläppscertifikat och från 2034 tas dessa bort i sin helhet. För cementtillverkare blir konsekvensen att man måste investera ytterligare i användning eller lagring av koldioxid för att hålla cementpriserna på en rimlig nivå.
Det är bakgrunden till att SCHWENK, inom ramen för projektet Catch 4 Climate (C4C) bygger en demoanläggning vid fabriken i Mergelstetten, Tyskland, för att både kunna ”fånga in” koldioxid för lagring alternativt för användning direkt vid produktion av syntetiskt bränsle. Facktermen är Oxyfuelförbränning.
Vid förbränningen används rent syre i stället för luft. Det resulterar i rökgaser med en koldioxidhalt på upp till 95 procent i stället för 25-30 procent i luft. Denna avskiljning av koldioxid blir mycket enklare eftersom det inte längre behövs en separering av koldioxid från kväve och andra rökgaser.
Flytande koldioxid är planerad att användas för tillverkning av syntetiskt bränsle till flygindustrin. Projektet är mycket kostnadskrävande och därför har fyra cementillverkare ingått partnerskap på området: SCHWENK, Heidelberg Materials, Dyckerhoff och Vikat samt anläggningsföretaget Polysius.
– Satsningen på den tyska demoanläggningen måste göras för framtiden. Slutmålet är koldioxidneutral cement och investeringar på befintliga produktionsanläggningar ska göras för att möta framtida krav och mål, summerar Tomasz Borowiec.
*Viridiscement: CEM II/B-M (S-LL) 52.5 N
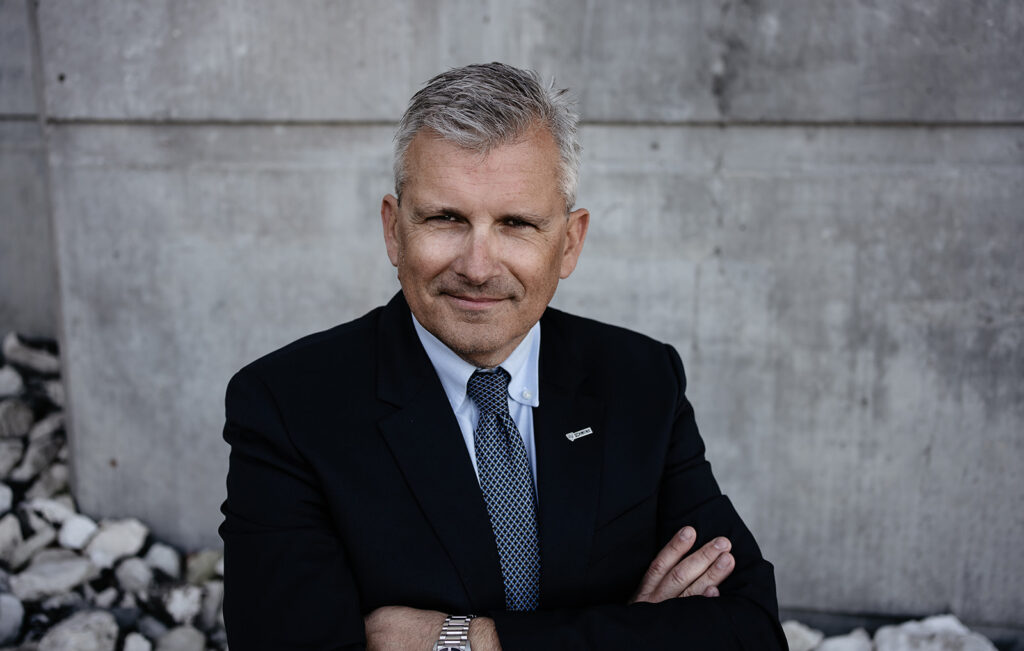
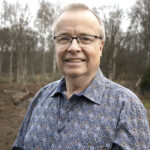